Why Plant Managers Struggle with Fluctuating Manpower Demand in Manufacturing
Plant managers face tough challenges in an increasingly competitive market. From the surging demand during industry-specific busy seasons to supply chain disruptions within the production team. On top of that, global and economic shifts like the pandemic, inflation, and natural disasters can affect profitability.
One of the biggest concerns for plant managers is finding reliable and strong staffing support. While general staffing agencies can help fill workforce gaps, they often struggle to keep up with the growing demands of the manufacturing industry.
By understanding the staffing challenges in manufacturing, identifying key opportunities, and applying the practical strategies covered in this blog, you can streamline manufacturing operations and lead more effectively as a plant manager.
Table of Contents
- What is the Major Weakness of Manufacturing?
- Common Manpower Challenges in the Manufacturing Industry
- High Turnover Rates
- Skills Gap
- Limited Access to a Wide Talent Pool
- The Impact of Manpower Demand Fluctuations in Manufacturing
- Why General Staffing Agencies Often Fall Short in Manufacturing
- The Need for Industry-Focused Staffing Solutions in Manufacturing
- What You Should Look for in a Staffing Partner
- Industry Experience
- Speed and Flexibility
- Recruitment and Training Process
- Performance Management
- Regulatory Compliance
- Conclusion
What is the Major Weakness of Manufacturing?
Skilled labor shortages have become a pressing concern that ultimately weakens the manufacturing sector. A recent study from the Congressional Policy and Budget Research reveals that within the industry sector, manufacturing experienced the most significant drop in employment at 4.3%.
Labor Shortage: A Major Concern of the Manufacturing Sector
As many experienced workers retire without sufficient numbers of trained replacements entering the field, labor shortage will not only affect production capabilities but also negatively impact the overall quality of products.
“To tackle the labor shortage effectively, manufacturing leaders must focus on improving frontline communication through digital technologies like connected workforce platforms, which provide the systems essential to helping workers perform their jobs faster and more successfully, remove obstacles, and enhance overall productivity.” – L2L CEO John Davagian
Common Manpower Challenges in the Manufacturing Industry
When demand fluctuates, so does the need for a workforce in the labor market. Even if new workers are brought in quickly, training takes time—and in manufacturing, that delay can harm productivity.
The manufacturing sector currently faces a serious manpower challenge, marked by:
High Turnover Rates
These challenges don’t just delay production—they also put extra pressure on the existing team, leading to decreased morale and productivity. The constant turnover means recruitment efforts will go around in a cycle of hiring and training, which can be both time-consuming and can potentially increase labor costs.
Skills Gap
New hires often require extensive training and skill development before they can contribute effectively to the operations. This onboarding period can slow down production and make it even harder to meet demand, adding to the workforce challenges plant managers already face.
Limited Access to a Wide Talent Pool
As demand for manufacturing production fluctuates, it’s becoming harder for companies to find and keep skilled workers with the right experience. This scarcity of skilled labor in manufacturing not only hinders growth but also impacts a company’s ability to innovate processes and remain competitive.
The Impact of Manpower Demand Fluctuations in Manufacturing
Manufacturing is no longer a steady predictable operation. Many businesses are now facing workforce challenges including:
Demand often rises and falls with the retail calendar, especially in industries like food, packaging, and electronics.
This approach, often called lean manufacturing or lean production, focuses on making only what’s needed, exactly when customers need it.
Geopolitical issues or port congestion can delay the delivery of raw materials, leading to backlogs in production schedules.
During periods of increased demand, companies may need to ramp up production, which often requires hiring additional workers or extending hours for existing employees.
As a plant manager, you can no longer afford to rely on inconsistent staffing. Fluctuating demand in manufacturing manpower requires workforce agility—but that agility must come from specialization, preparation, and deep industry knowledge.
Why Partnering with a Service Provider Can Improve Your Business
Building strategic partnerships empowers businesses to develop unique services that competitors cannot imitate. Learn why partnering with a service provider for manpower can improve your business.
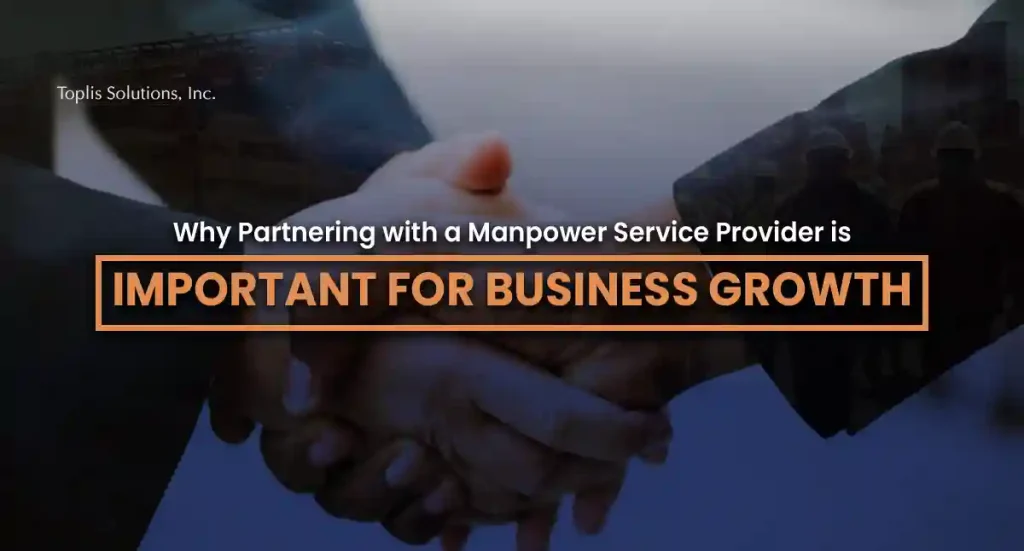
Why General Staffing Agencies Often Fall Short in Manufacturing
General staffing agencies face significant limitations that can hinder their effectiveness, especially in industries like manufacturing. These reasons include:
Many general staffing agencies may not fully understand the unique demands and nuances of manufacturing roles, which can lead to mismatches between candidates and job requirements. As a result, they may send candidates who aren’t a good fit—people who lack the experience to keep up with demanding production tasks.
In manufacturing, workers need to be accurate and fast to adapt to the fast-paced environment. Without proper training processes tailored to industry standards, staffing agencies may place underqualified individuals into critical positions. This can lead to errors and downtime in manufacturing operations.
Manufacturing companies often face sudden changes in demand. In such cases, they often require rapid scaling of workforce for urgent deployment. Unfortunately, general staffing agencies may not be equipped to respond quickly enough to these changes, which can cause delays and missed deadlines.
To overcome these limitations, leaders should consider partnering with specialized staffing solutions that focus on their specific industry needs. By doing so, they can ensure a more effective hiring process that aligns with their goals.
The Need for Industry-Focused Staffing Solutions in Manufacturing
What you truly need as a plant manager is more than just a general staffing agency but a service provider with deep expertise in the manufacturing sector. A workforce provider like Toplis Solutions acts as an extension of your operations team, not just a source of temporary labor.
Here’s what sets Toplis apart:
- Pre-trained and Job-Ready Workers – Deep familiarity with operational protocols, production lines, and safety measures.
- On-site Coordinators – Representatives ready to supervise, guide, and optimize labor deployment in real-time.
-
Scalability- Ability to deploy different workers on short notice during demand peaks.
-
Compliance and Quality Monitoring – Ensures every deployed worker meets your standards from the start to the end of every project.
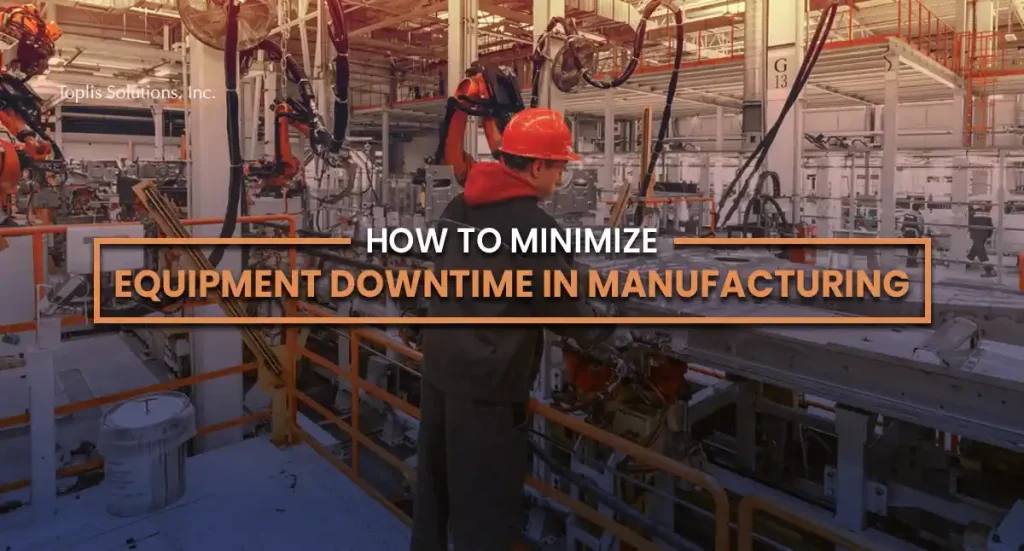
How to Minimize Equipment Downtime in Manufacturing
Explore seven smart tips to cut down equipment downtime in manufacturing. Learn how to avoid breakdowns, improve productivity, and make your operations run smoother.
What You Should Look for in a Staffing Partner
Choosing the right staffing partner is a strategic decision for plant managers. To keep operations running smoothly, it’s important to follow a clear set of guidelines. After all, a manpower service that aligns with your objective is key to a successful and efficient operation.
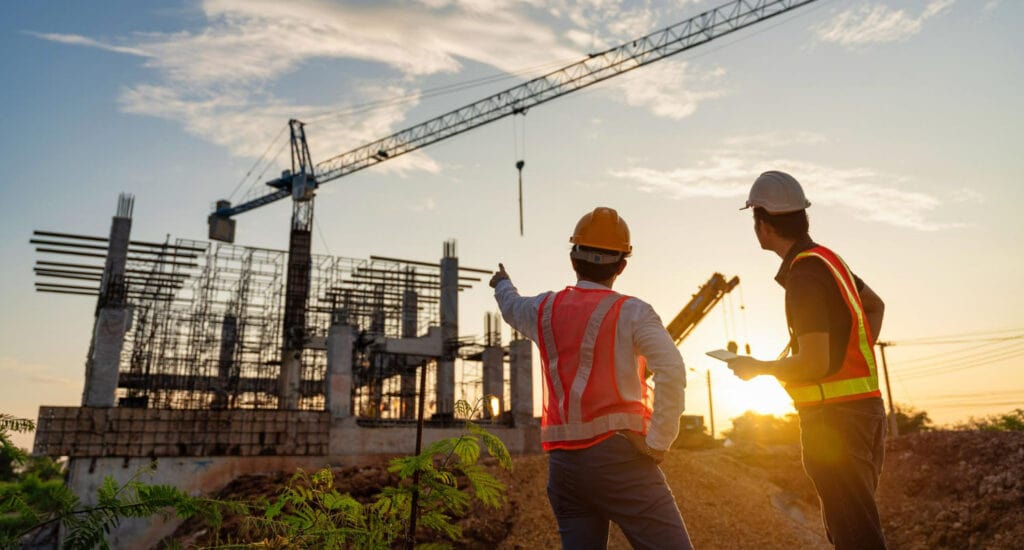
1. Industry Experience
A staffing partner with a deep understanding of the challenges in manufacturing sector will not only understand the specific skills needed but also the potential challenges faced in this environment. Look for a manpower provider who has worked with manufacturers similar to your business—whether in automotive, food processing, FMCG, or electronics.
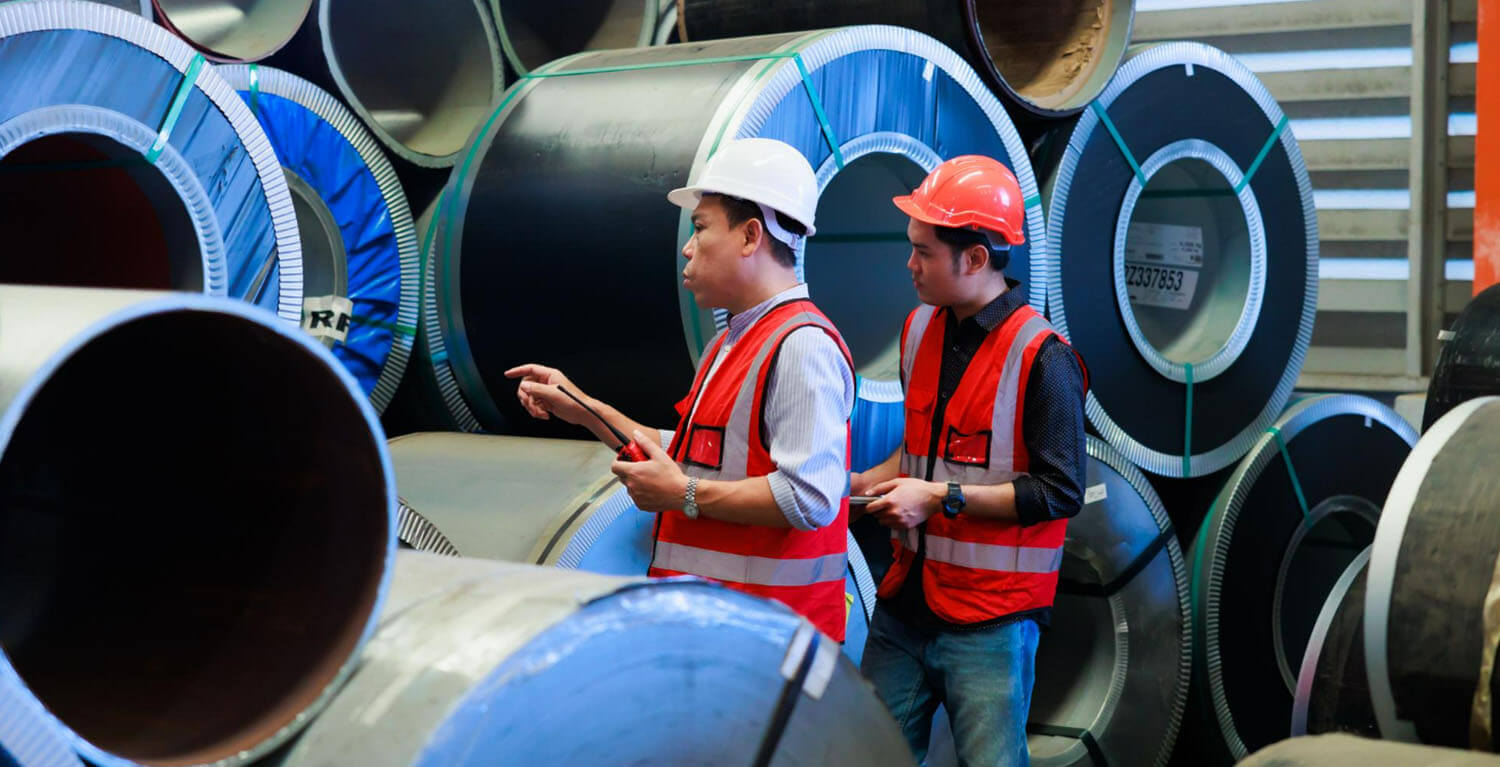
2. Speed and Flexibility
Assess their ability to scale up manufacturing staffing solutions. Do they offer support during peak production cycles? Considering how unpredictable the manufacturing landscape can be, your staffing partner should demonstrate adaptability to shifting demands or urgent requirements without compromising on service quality.
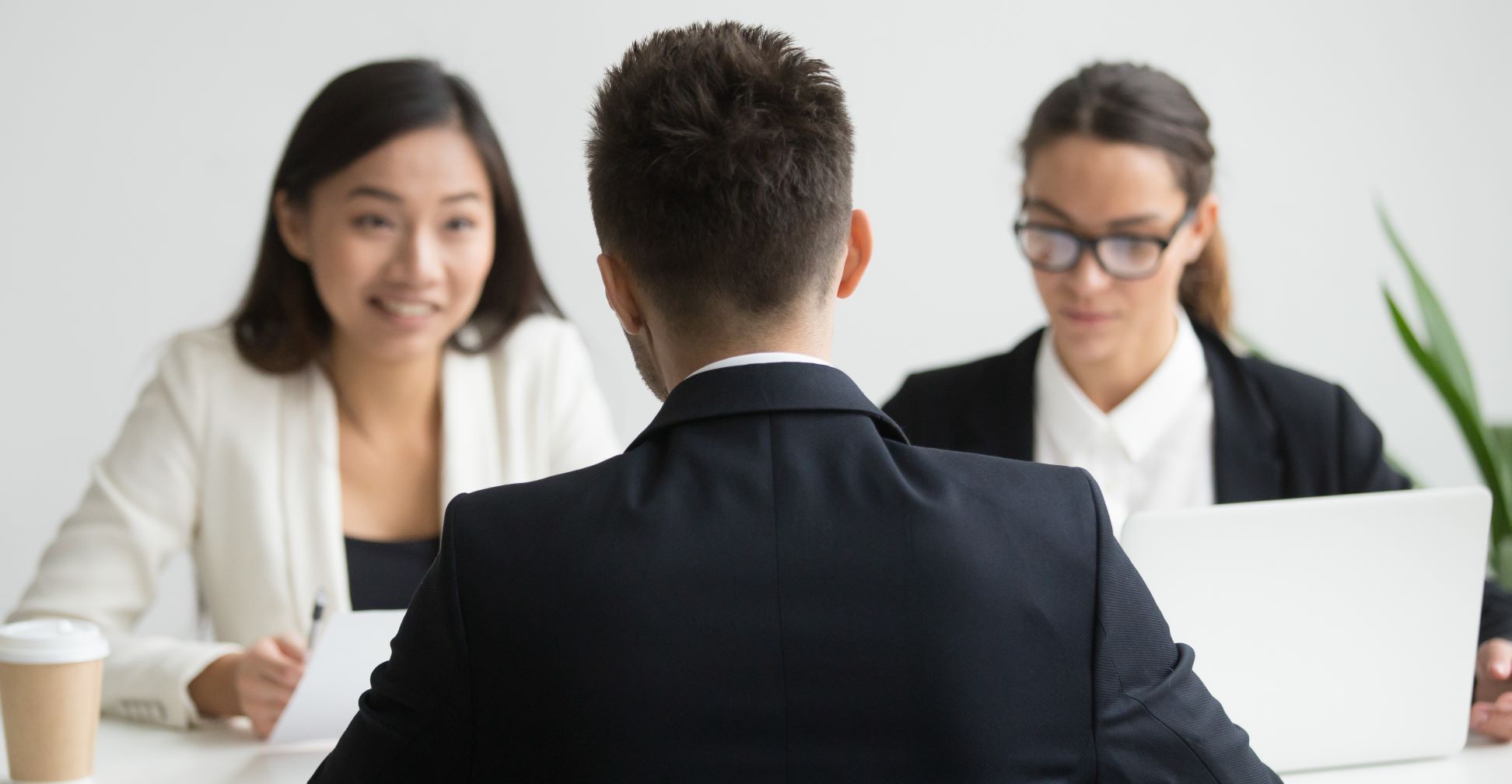
3. Recruitment and Training Process
A strong screening process is important for identifying qualified candidates with both technical skills and cultural fit for your business. Make sure your service provider gives basic safety and productivity training before sending anyone on-site.
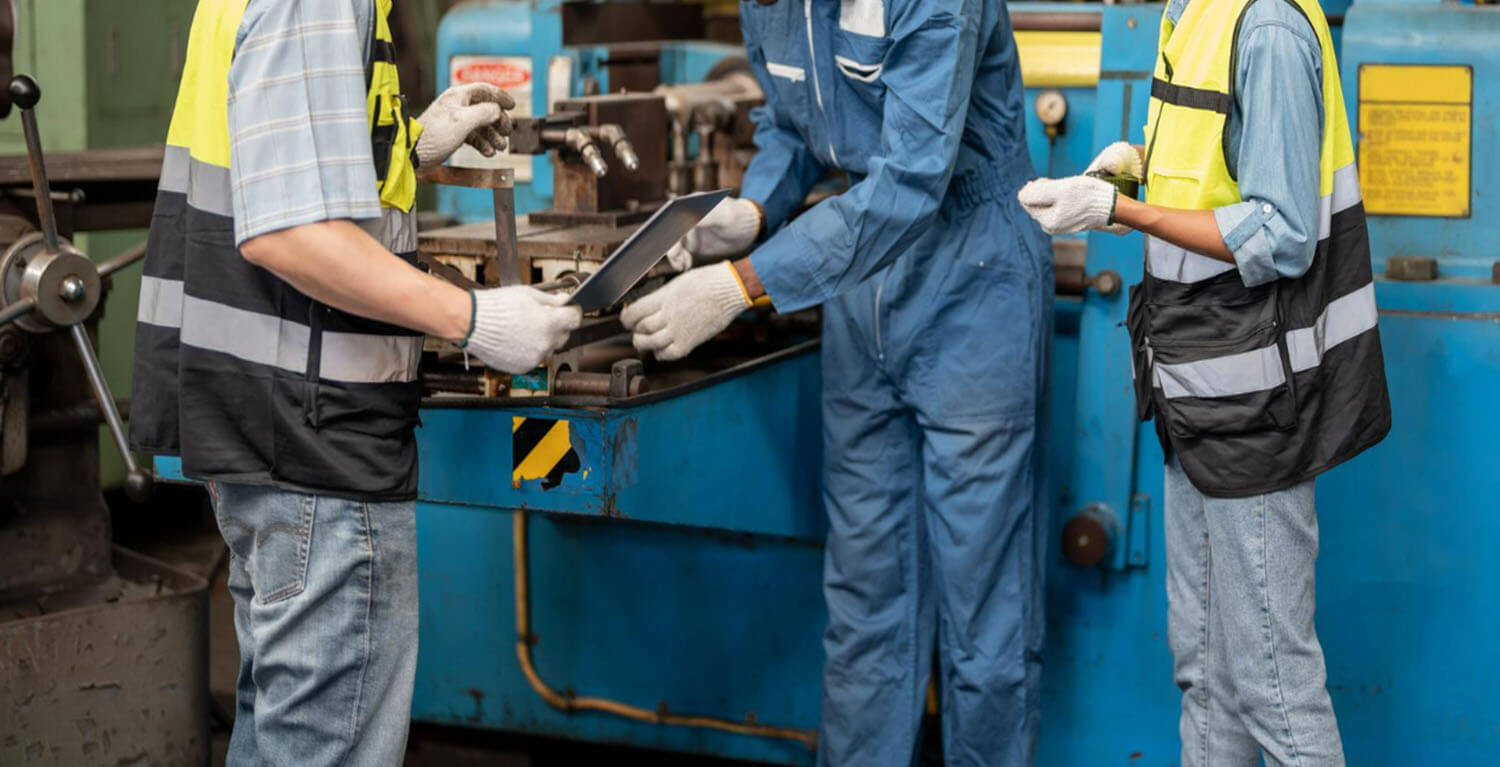
4. Performance Management
The right service provider will track key metrics like attendance, productivity, and employee retention. This data helps you make smarter operational decisions. Over time, it not only supports worker development but also improves your business’ performance.
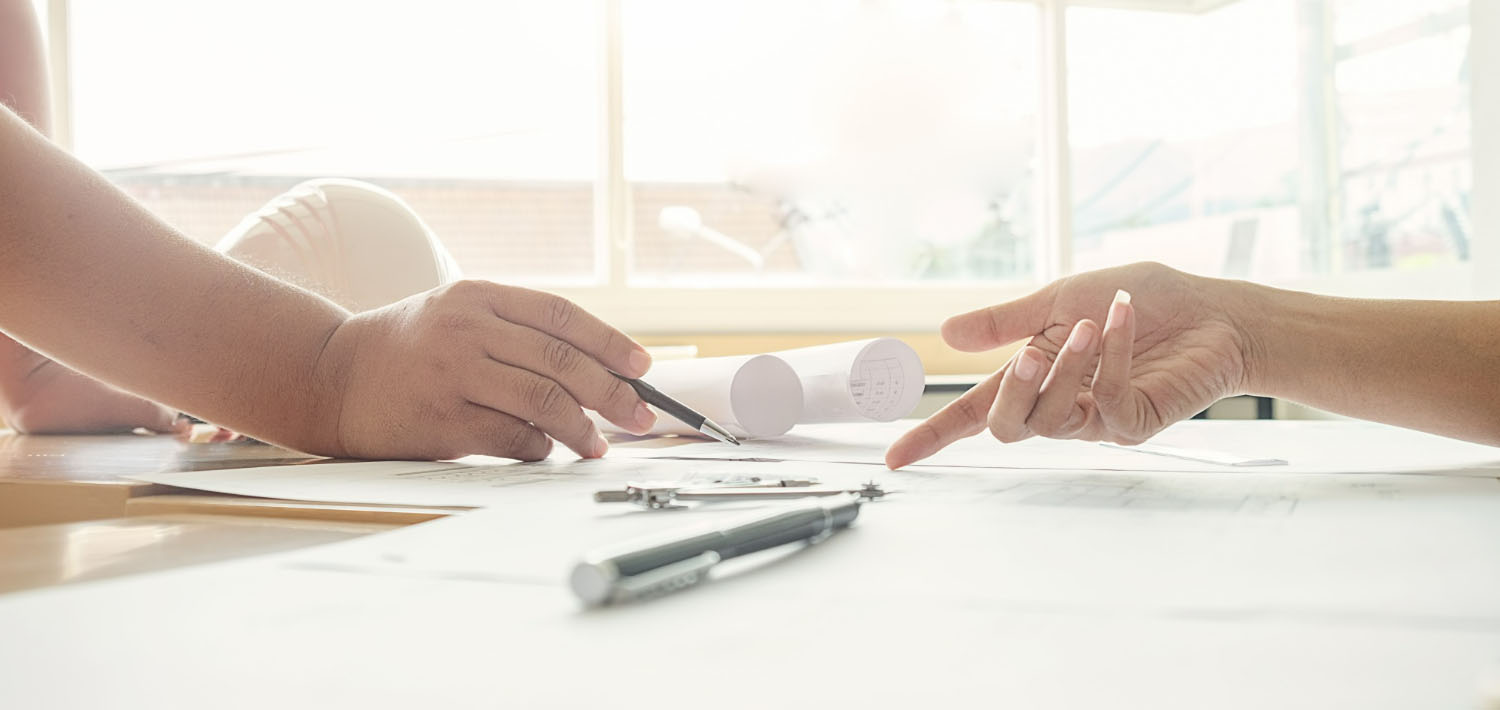
5. Regulatory Compliance
Ensure your service provider follows local laws, safety requirements, and labor deployment guidelines to protect your business. Aside from staying compliant, this practice boosts your operations, reduces legal risks, and allows your business to stay ahead of the competition.
Conclusion
Managing a manufacturing workforce effectively is key to maintaining stability and achieving long-term business success. While general staffing can provide short-term headcount, they often fall short in tools and ability to thrive in complex environments.
To effectively navigate these challenges, consider establishing business partnerships with service providers that have real manufacturing experience. By collaborating with industry experts, you can scale your manufacturing workforce more effectively.
Take the Next Step with Toplis Solutions
Is your current staffing partner helping you meet production targets—or creating more work for your team? Toplis proactively addresses these challenges, so you can better navigate your business!
PARTNER WITH A SERVICE PROVIDER THAT UNDERSTANDS YOUR BUSINESS