Manufacturing downtime is any period when a production line stops abruptly mid-operation. This often happens due to equipment breakdowns, scheduled maintenance, or problems with labor and supply chains.
According to a 2021 report by ServiceMax, 82% of manufacturing businesses experienced downtime. This shows that downtime is a common challenge in the manufacturing industry.
In this blog, you’ll find seven smart tips to cut down equipment downtime in manufacturing. Learn how to avoid breakdowns, improve productivity, and make your operations run smoother.
We’ll share easy-to-follow strategies to reduce both unplanned and planned downtime. These tips will help boost your equipment’s performance, increase work order output, and keep costs under control.
Table of Contents
- Why Downtime Is the Silent Profit Killer in Manufacturing Operations
- Understanding the Causes of Downtime in Production
- Equipment failures
- Supply delays
- Human error
- Missed maintenance
- Lack of real-time data
- 7 Strategies to Minimize Equipment Failure in Manufacturing
- Implement Preventive Equipment Maintenance Program
- Investing in Equipment Monitoring Sensors
- Conduct Training in Production Line Teams
- Establish Standard Operational Procedures
- Adopting Lean Manufacturing to Increase Uptime
- Improve Supplier Coordination
- Analyze Historical Data to Reduce Equipment Downtime
- Conclusion

Why Downtime Is the Silent Profit Killer in Manufacturing Operations
Every minute of production delay means lost revenue. When machines stop working or the production process slows down, it can affect the entire manufacturing manpower operations.
Repair and maintenance costs fluctuate according to market demands. Meanwhile, constant breakdowns and delays can frustrate employees. Over time, this can lead to low engagement and a higher turnover rate.
But how bad is it for your operations? Let’s break it down.
What Are the Real Costs of Downtime?
Delays Productivity
A single hour of downtime can stop your whole line
Increases Costs
From emergency repairs to rush orders, unexpected costs can pile up fast
Affects Employee Morale
Frequent breakdowns frustrate teams, leading to stress and higher turnover rates
To avoid these problems, manufacturers should focus on reducing downtime. Regular equipment checks, employee training, and the use of modern technology can all help improve efficiency. These steps not only cut costs but also keep workers motivated and aligned with company goals.
Understanding the Causes of Downtime in Production
To keep operations running smoothly, it’s important to know what causes production delays. Here are some of the common reasons why manufacturing industry faces issue of downtime
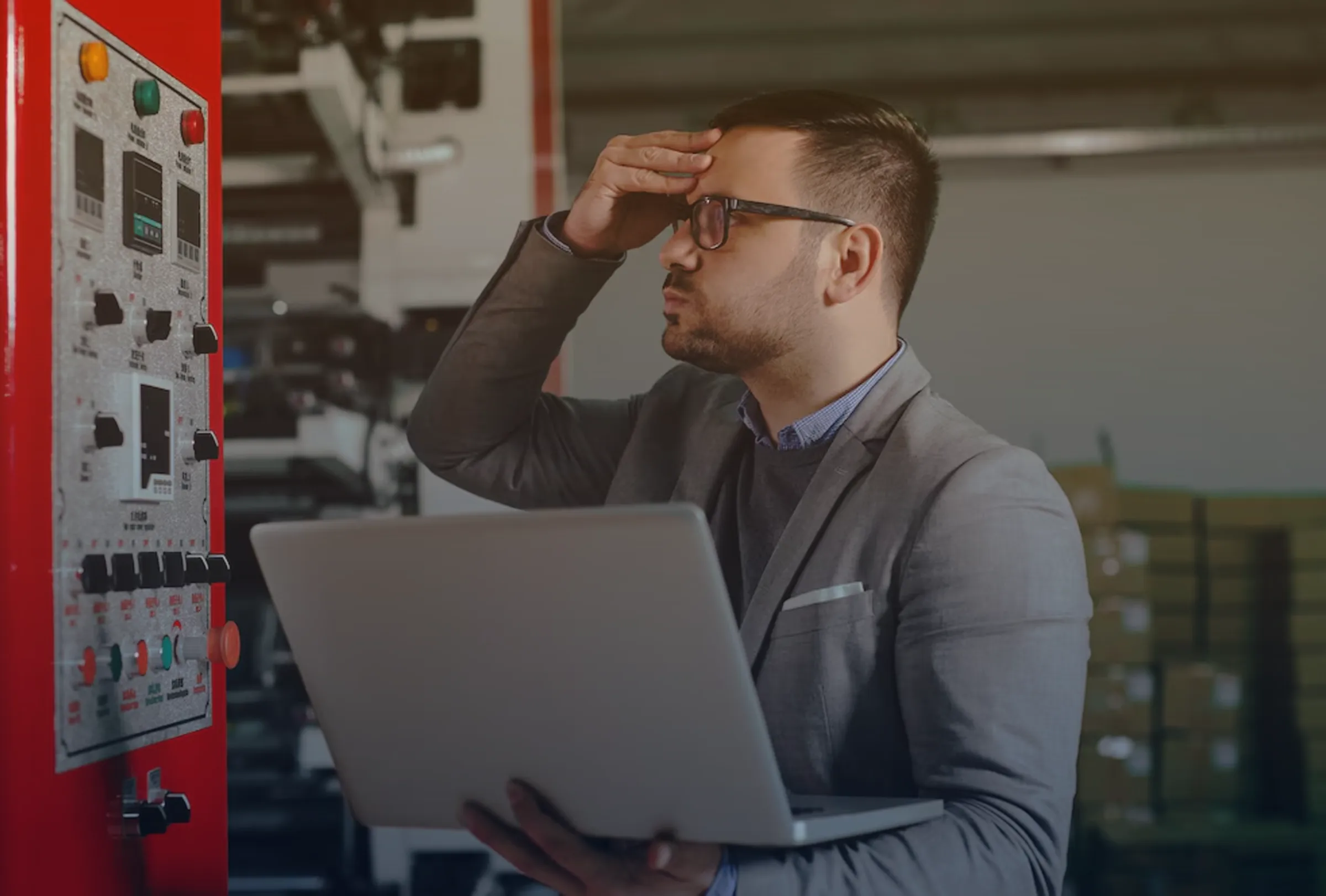
Equipment Failures
When machines break down without warning, production stops. This leads to delays and lost revenue. The best way to avoid this is to follow a regular maintenance schedule. Establish preventive maintenance in manufacturing to catch problems early.
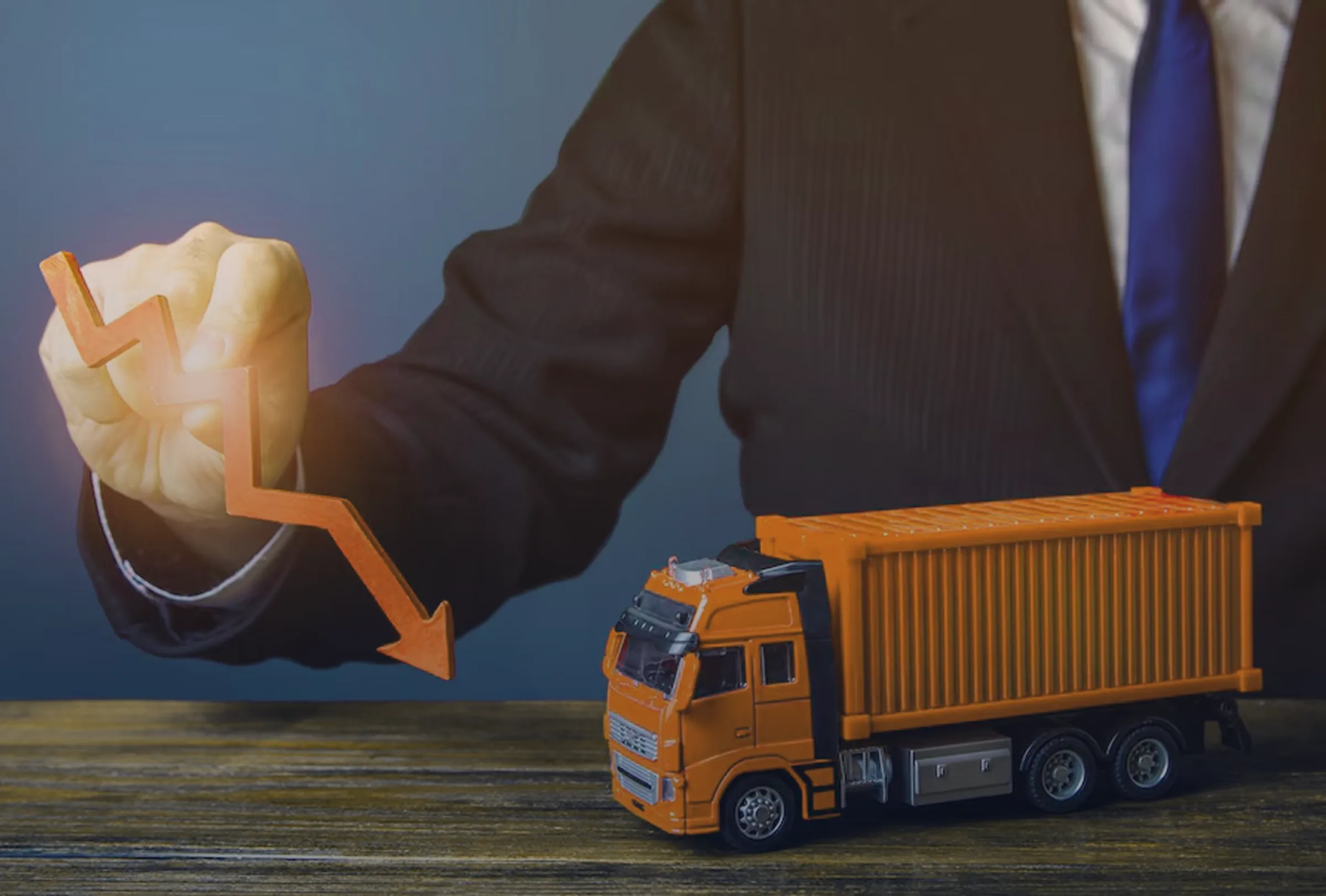
Supply Delays
Production lines rely on the steady flow of raw materials. If supplies don’t arrive on time, operations come to a halt. Building strong partnerships with suppliers and having backup sources can reduce this risk.
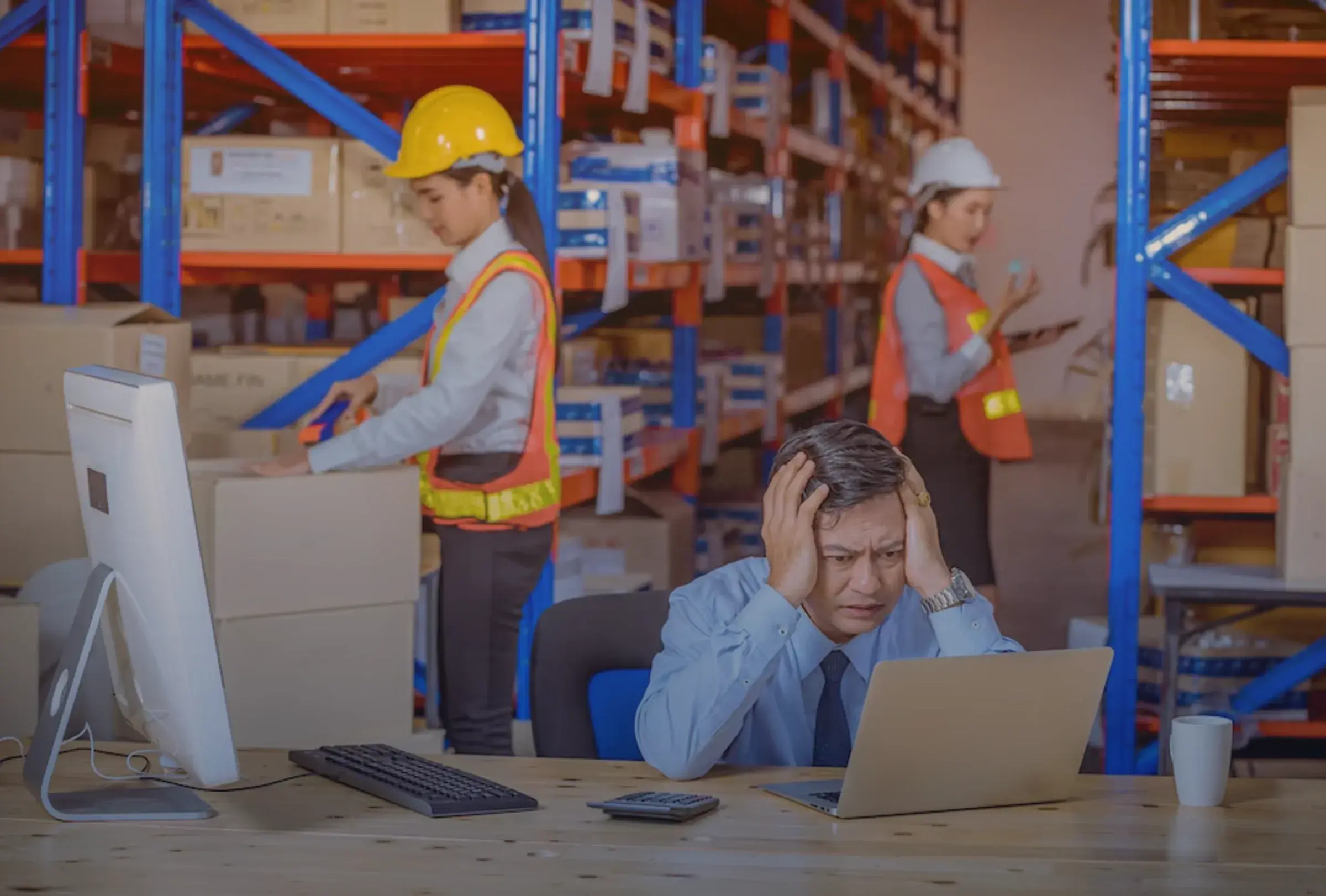
Human Error
Mistakes during machine setup or operation can cause delays. Training maintenance teams and fostering accountability can help prevent these issues from affecting production schedules.
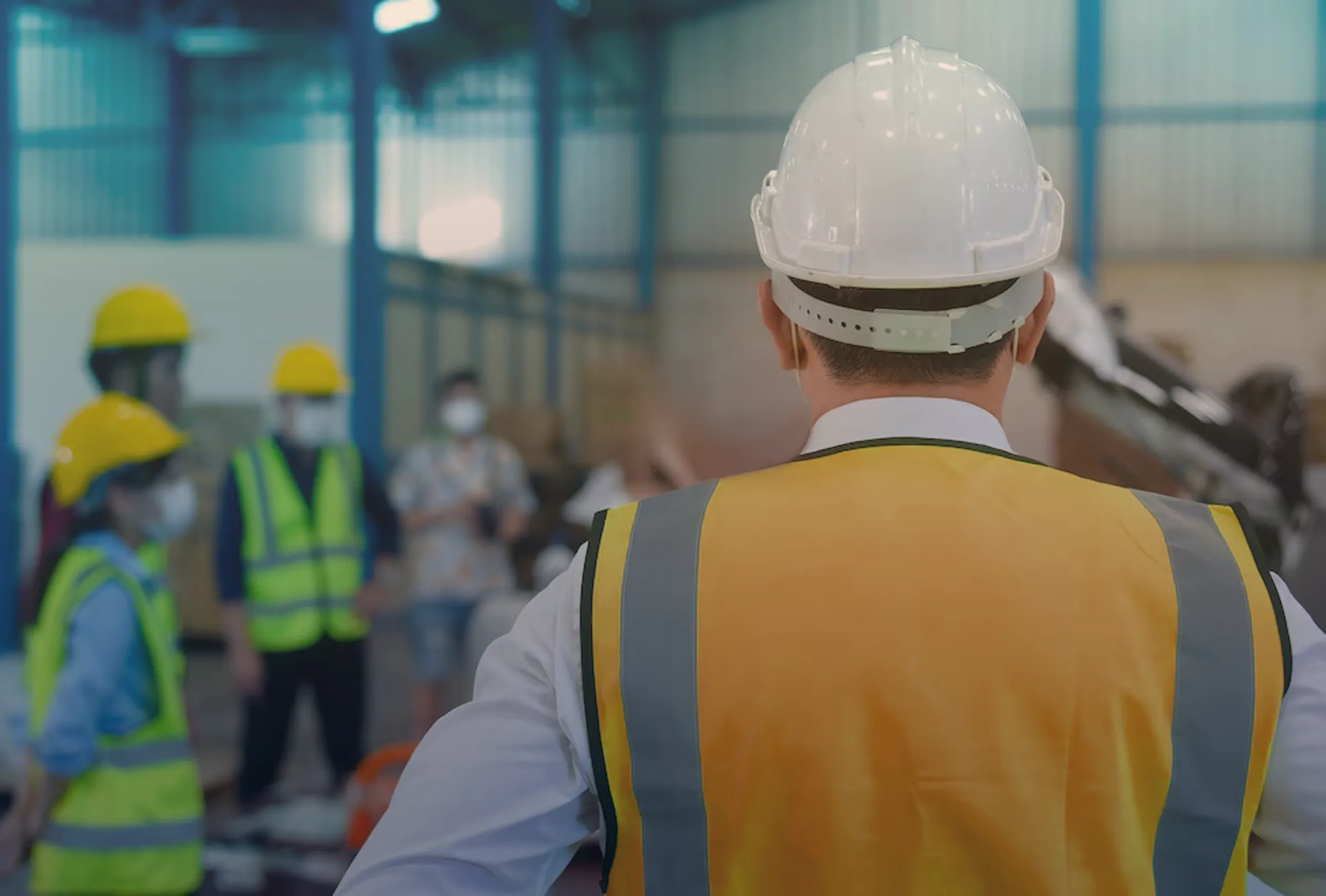
Missed Maintenance
Skipping routine maintenance or ignoring small issues can lead to bigger equipment failures. Scheduled servicing should always be a top priority to keep everything running smoothly.
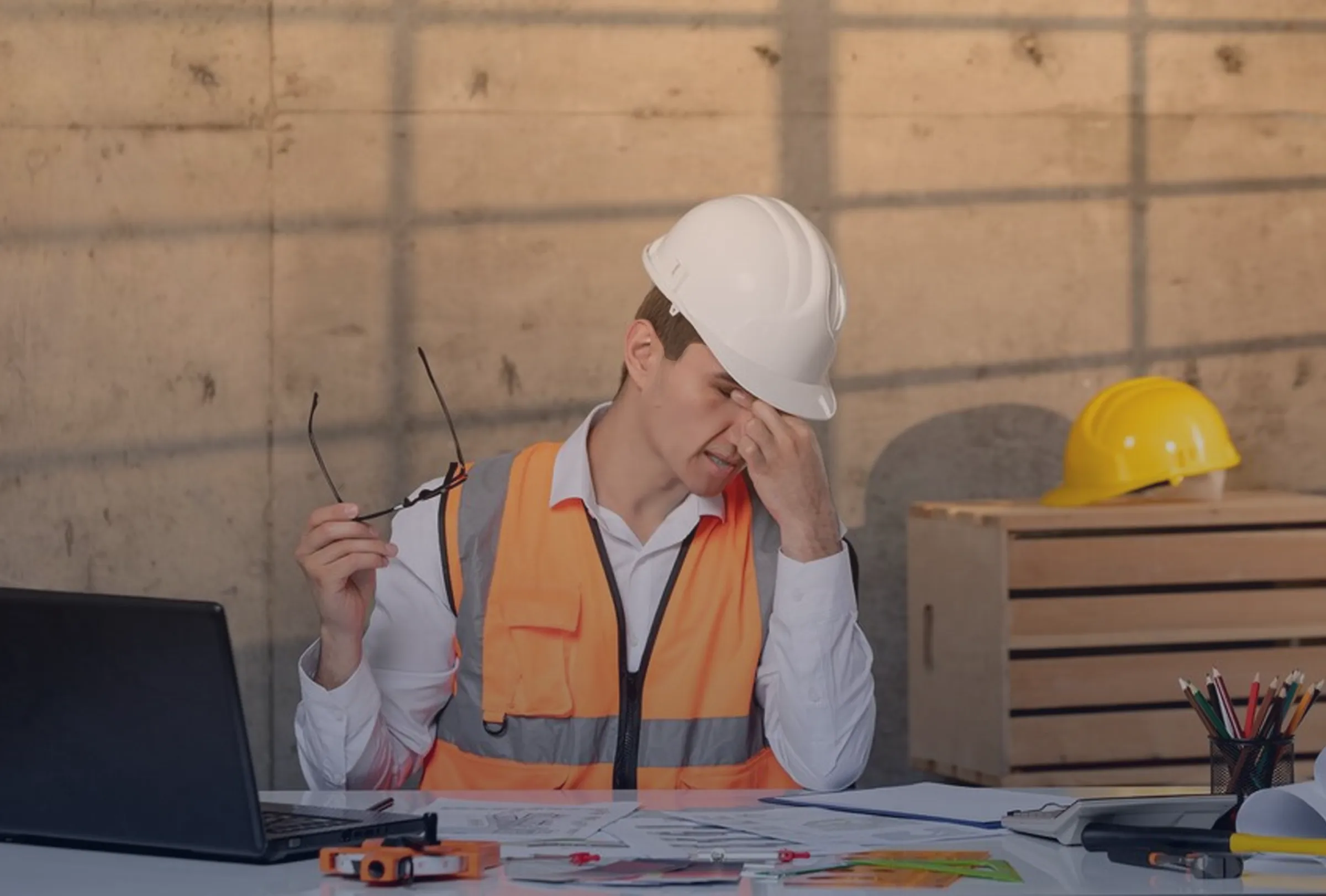
Lack of Real-Time Data
Without real-time data, it’s hard to spot problems before they happen. This results in poor visibility into equipment performance, which can increase downtime. You can address this by using advanced tools to better control and strengthen your predictive maintenance action plans.
Dive Deeper into Toll Manufacturing
Curious about how toll manufacturing works and how it can benefit your business? Check out our latest blog to understand the process, key advantages, and how it can optimize your production.
Explore everything you need to know about toll manufacturing and how it can help your business thrive.
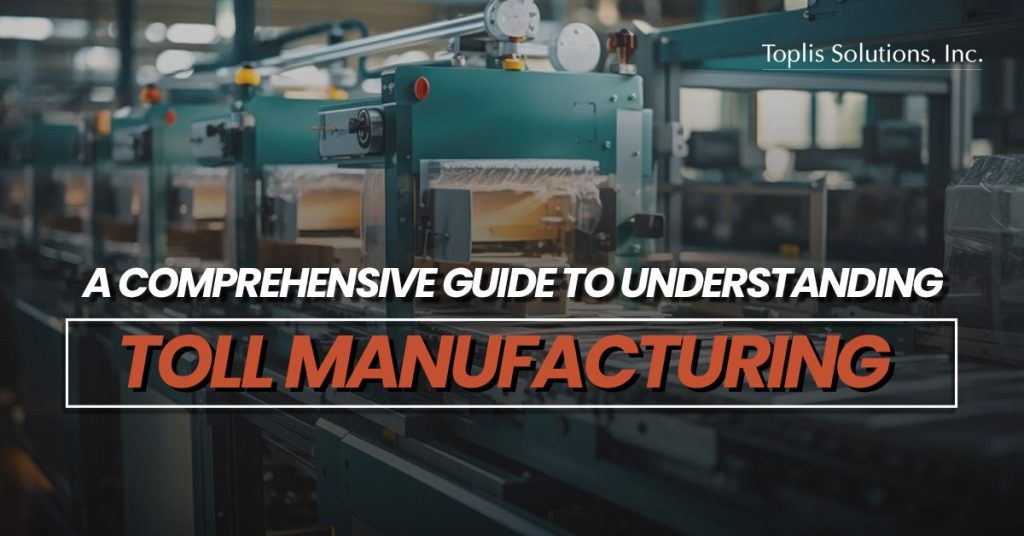
7 Strategies to Minimize Equipment Failure in Manufacturing
1. Implement Preventive Equipment Maintenance Program
Implementing scheduled checks in workflow can increase efficiency and streamline operations. By setting aside dedicated time for regular evaluations, teams can proactively identify potential issues before they escalate into larger problems. This saves both time and resources, as fixing small issues early is much cheaper than handling bigger problems later.
2. Investing in Equipment Monitoring Sensors
The ability to catch early signs of machine failure can be a game-changer. Investing in sensors in manufacturing is not an additional expense but a necessity. They offer real-time analytics to help manufacturers monitor equipment performance. This can help find potential issues before they cause unexpected downtime
3. Conduct Training in Production Line Teams
Empowering workers with quick troubleshooting knowledge is important for any production line aiming for efficiency and excellence. Comprehensive training programs that focus on practical troubleshooting help employees enhance their overall productivity.
This proactive approach not only minimizes downtime but also fosters a culture of problem-solving and innovation among employees. When they feel capable of handling challenges independently, their confidence grows, which translates into better performance.
4. Establish Standard Operational Procedures
SOPs provide a clear and consistent way to handle daily tasks and maintenance work. They help reduce mistakes and lower the chances of machine failure caused by human error. Regular updates to SOPs based on best practices will increase production and make the process more sustainable for manufacturers.
5. Adopting Lean Manufacturing to Increase Uptime
Lean manufacturing boosts efficiency by removing waste that uses up resources without adding value to the service.
Specific examples of lean waste include:
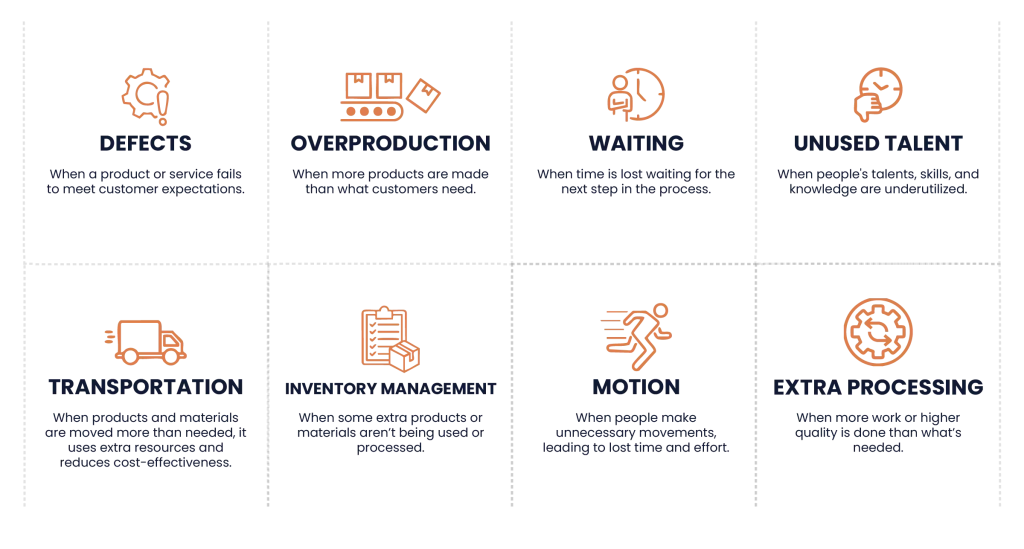
Adopting lean manufacturing helps reduce all types of waste and boosts customer satisfaction, which can lead to more business transactions. It also shifts people’s mindsets and helps overcome mental blocks by encouraging creative, out-of-the-box thinking.
6. Improve Supplier Coordination
Coordination with suppliers helps reduce downtime by making sure materials will arrive on time. This cuts the need for extra inventory and improves production planning, leading to a smoother workflow with fewer delays.
7. Analyze Historical Data to Reduce Equipment Downtime
Using gathered data allows manufacturers to easily identify patterns, predict potential problems, and provide maintenance plans before issues happen. This helps avoid unplanned downtime, boosts efficiency, and provides real-time information for faster problem-solving and decision-making.
Key metric indicators determine the effectiveness of the processes implemented by manufacturers. Some KPIs that you can consider are the following:
Mean Time Between Failures (MTBF): The average time an equipment runs before it breaks down.
Mean Time To Repair (MTTR): Measures the typical duration it takes to repair a piece of equipment once it malfunctions.
Overall Equipment Effectiveness (OEE): A key metric that measures equipment effectiveness by tracking its availability, performance, and output quality.
Conclusion
The benefits of reducing downtime in manufacturing are clear, to increase efficiency and prevent production delays.
Minimizing downtime is key to improving productivity, lowering costs, and keeping workers motivated. By knowing what causes delays, manufacturers can take action to stop them early.
Simple steps like regular maintenance, real-time monitoring, staff training, and lean practices can make production more efficient. Better coordination with suppliers and using data to guide decisions also help avoid slowdowns. With the right tools and support from Toplis Solutions, manufacturers can maintain smooth operations and meet customer demands on schedule.
Keep Your Manufacturing Facility Running Smoothly with Our Expert Team
Is downtime slowing down your manufacturing process? Get expert support to streamline operations and boost your production line. At Toplis Solutions, we provide customized production support that keeps your equipment running smoothly.
DISCOVER HOW WE CAN HELP YOU